Choosing a Zinc Alloy
Topic: Zinc Alloy Choices
After determining that a zinc alloy is right for your die casting application, the next question is often: which alloy should I use? There are several determining factors, however using the following guidelines will make the choice simple:
Zamak 3
The most common zinc die casting alloy in North America. Often the first choice when considering an alloy for zinc die casting due to its excellent combination of mechanical and physical properties, and superb casting and finishing ability.
Zamak 2
Within the Zamak family of alloys, Zamak 2 has the highest strength and hardness due to its higher copper content (3%). Also known as Kirksite when making tooling for the stamping or plastic injection mold industries.
Zamak 5
Commonly used zinc die casting alloy throughout the world due to its combination of strength, ductility and fluidity. The 1% additional copper added to the alloy improves the alloy’s mechanical properties.
Zamak 7
Although magnesium is a useful element to combat corrosion effects of the alloy due to certain impurities, it was also found to reduce the alloy’s fluidity. In this alloy, nickel replaced magnesium, which helped improve the fluidity and casting ability of the alloy. The properties are similar to Zamak 3 with enhanced fluidity.
ZA-8
Zinc alloy with 8% aluminum. The most common of the ZA alloys due to its combination of strength, casting ability (cast in a hot chamber machine), and is often electro-plated.
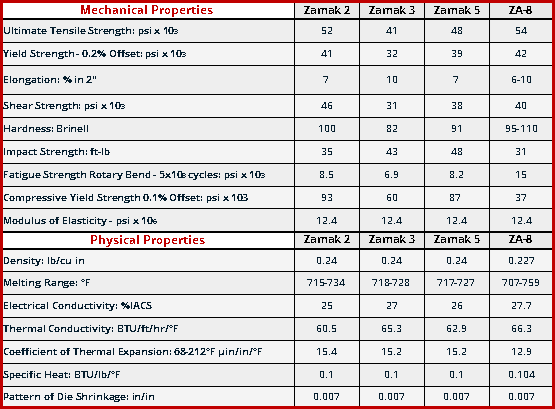
For additional specifications or to speak with an expert, please contact us a sales@castproducts.com
* Information courtesy of Eastern Alloys
Back To Blog